Koko kone on perusyksikköventtiiliKokoonpano ja useat osat muodostavat venttiilin osat (kuten venttiilin konepelli, venttiililevy jne.). Useiden osien kokoonpanoprosessia kutsutaan komponenttikokoonpanoksi, ja useiden osien ja komponenttien kokoonpanoprosessia kutsutaan kokonaiskokoonpanoksi. Kokoonpanotyöllä on suuri vaikutus tuotteen laatuun. Vaikka suunnittelu on tarkka ja osat ovat päteviä, jos kokoonpano on väärä, venttiili ei täytä määräysten vaatimuksia ja johtaa jopa tiivistymiseen.
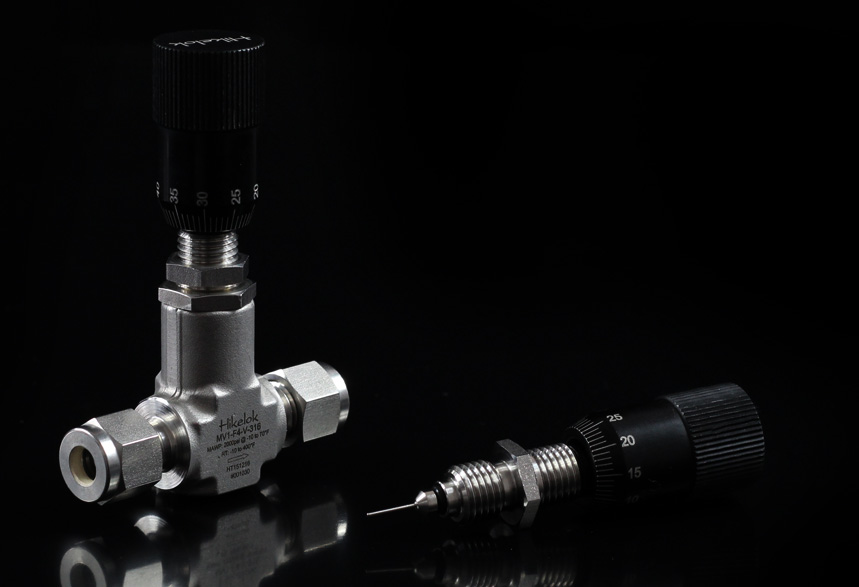
Venttiilien kokoonpanoon on kolme yleistä menetelmää, nimittäin täydellinen vaihtomenetelmä, rajoitettu vaihtomenetelmä, korjausmenetelmä.
Täydellinen vaihtomenetelmä
Kun venttiili kootaan täydellisellä vaihtomenetelmällä, jokainen venttiilin osa voidaan koota ilman korjausta ja valintaa, ja tuote voi täyttää määritetyt tekniset vaatimukset kokoonpanon jälkeen. Tällä hetkellä venttiilien osat olisi käsiteltävä täysin suunnitteluvaatimusten mukaisesti mittasuunnitelman ja geometrisen toleranssin vaatimusten täyttämiseksi. Koko vaihtomenetelmän edut ovat: kokoonpanotyö on yksinkertaista ja taloudellista, työvoima ei tarvitse korkeaa taitoa, kokoonpanoprosessin tuotantotehokkuus on korkea, ja kokoonpanolinjan ja ammatillisen tuotannon järjestäminen on helppo . Ehdottomasti puhumista, kun suoritetaan täydellinen varauskokoonpano, osien koneistustarkkuuden on kuitenkin oltava korkeampi. Se sopii maapalloventtiiliin, takakortin, palloventtiiliin ja muihin venttiileille, joissa on yksinkertainen rakenne ja pieni ja keskisuuri halkaisija.
Rajoitettu vaihtomenetelmä
Venttiili on koottu rajoitetulla vaihtosuunnitelmalla, ja koko kone voidaan käsitellä taloudellisen tarkkuuden mukaan. Kokoamisen yhteydessä voidaan valita tietty koko säätö- ja kompensointivaikutus määritetyn kokoonpanotarkkuuden saavuttamiseksi. Valintamenetelmän periaate on sama kuin korjausmenetelmä, mutta tapa muuttaa kompensointisormuksen kokoa on erilainen. Ensimmäinen on muuttaa kompensointirenkaan kokoa valitsemalla lisävarusteet, kun taas jälkimmäinen on muuttaa korvausrenkaan kokoa leikkaamalla tarvikkeita. Esimerkiksi: Yläydin ja säätöventtiilin tyyppisen kaksoisram -kiilan porttiventtiilin tiivisteen yläosaa, jaetun palloventtiilin kahden kappaleen välinen säätö tiiviste on valita erityiset osat kompensointiosiksi mittaketjuun liittyvässä muodossa kokoonpanotarkkuuteen ja saavuta vaadittu kokoonpanotarkkuus säätämällä tiivisteen paksuutta. Jotta varmistetaan, että kiinteät kompensointiosat voidaan valita eri tilanteissa, on välttämätöntä valmistaa joukko pesukone- ja akseliholkkien kompensointiosia, joiden paksuus ja koko on etukäteen hydraulisen ohjausventtiilin mallin valinnan suhteen kokoonpanon aikana.
Korjausmenetelmä
Venttiili kootaan korjaamalla menetelmä, osat voidaan käsitellä taloudellisen tarkkuuden mukaan, ja sitten tietty koko säätö- ja kompensointivaikutus voidaan korjata kokoonpanon aikana määritetyn kokoonpanon tavoitteen saavuttamiseksi. Esimerkiksi kiilaporttiventtiilin portti ja venttiilin runko, koska vaihtovaatimukset toteuttavat korkeat prosessointikustannukset, useimmat valmistajat hyväksyvät korjausprosessin. Toisin sanoen portin tiivistyspinnan lopullisessa hiomisessa aukon koon ohjaamiseksi levy tulee sovittaa venttiilin rungon tiivistyspinnan aukon koon mukaan lopullisten tiivistysvaatimusten saavuttamiseksi. Tämä menetelmä lisää levyn sovitusprosessia, mutta yksinkertaistaa huomattavasti edellisen prosessointiprosessin mittatarkkuusvaatimuksia. Erityisen henkilöstön levyn sovitusprosessin ammattitaitoinen toiminta ei vaikuta koko tuotannon tehokkuuteen. Venttiilin kokoonpanoprosessi: Venttiilit kootaan erikseen kiinteään paikkaan. Osien ja komponenttien kokoonpano ja venttiilien yleiskokoonpano suoritetaan kokoonpanopajassa, ja kaikki tarvittavat osat ja komponentit kuljetetaan kokoonpanopaikalle. Yleensä kuinka monta työntekijäryhmää on vastuussa osien kokoonpanosta ja yleiskokouksesta samanaikaisesti, mikä ei vain lyhennä kokoonpanon sykliä, vaan myös helpottaa erityiskokoonpanotyökalujen soveltamista, ja sillä on alhaiset vaatimukset tekniselle tasolle tekniselle tasolle työntekijät.
Viestin aika: helmikuu-23-2022