Уся машына - самая асноўная адзінкаклапанЗбор, а таксама некалькі дэталяў складаюць дэталі клапана (напрыклад, капот клапана, дыск клапана і г.д.). Працэс зборкі некалькіх частак называецца кампанентнай зборкай, а працэс зборкі некалькіх частак і кампанентаў называецца Total Assembly. Праца зборкі аказвае вялікі ўплыў на якасць прадукцыі. Нават калі дызайн дакладная, а дэталі будуць кваліфікаваны, калі зборка будзе няправільнай, клапан не будзе адпавядаць патрабаванням правілаў і нават прывядзе да ўцечкі ўшчыльнення.
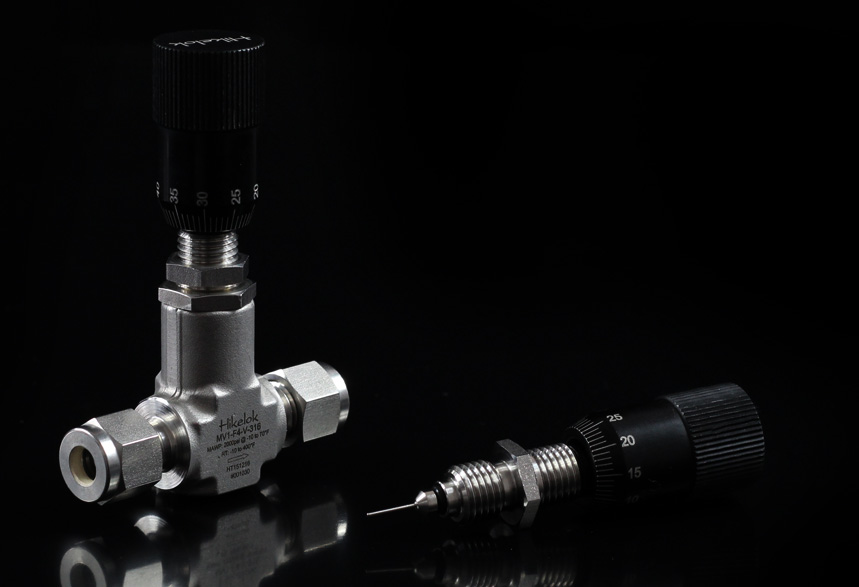
Існуе тры агульныя метады зборкі клапана, а менавіта - поўны метад развязкі, абмежаваны метад развязкі, метад рамонту.
Поўны метад развязкі
Калі клапан сабраны поўным метадам развязкі, кожная частка клапана можа быць сабрана без рамонту і выбару, і прадукт можа адпавядаць заданым тэхнічным патрабаванням пасля зборкі. У гэты час дэталі клапана павінны быць апрацаваны ў поўным аб'ёме з патрабаваннямі праектавання, каб адпавядаць патрабаванням дакладнасці вымярэння і геаметрычнай талерантнасці. Перавагі поўнага метаду абмену: праца зборкі простая і эканамічная, працоўнай сілай не патрэбна высокая ступень майстэрства, эфектыўнасць вытворчасці працэсу зборкі высокая, і лёгка арганізаваць зборачную лінію і прафесійную вытворчасць . Аднак абсалютна кажучы, калі будзе прынята поўная замена зборкі, дакладнасць апрацоўкі дэталяў павінна быць вышэйшай. Ён падыходзіць для глобуснага клапана, праверкі клапана, шаравага клапана і іншых клапанаў з простай структурай і невялікім і сярэднім дыяметрам.
Абмежаваны метад абмену
Клапан сабраны з абмежаваным метадам развязкі, і ўся машына можа быць апрацавана ў адпаведнасці з эканамічнай дакладнасцю. Пры зборцы для дасягнення зададзенай дакладнасці зборкі можа быць абраны пэўны памер з карэкціроўкай і эфектам кампенсацыі. Прынцып спосабу выбару такі ж, як у метадзе рамонту, але спосаб змены памеру кампенсацыйнага кольца адрозніваецца. Першы - змяніць памер кампенсацыйнага кольца, выбраўшы аксэсуары, а другі - змяніць памер кампенсацыйнага кольца, абрэзаўшы аксэсуары. Напрыклад: верхняе ядро і рэгуляванне пракладкі кіравання клапанам падвойнага клапана клінавых засаўкі, пракладкі, якая рэгулюецца паміж двума целамі раздзельнага шаравага клапана і г.д. да дакладнасці зборкі і дасягнуць неабходнай дакладнасці зборкі, адрэгулюючы таўшчыню пракладкі. Для таго, каб у розных сітуацыях можна было выбіраць фіксаваныя дэталі кампенсацыі, неабходна вырабляць набор дэталяў кампенсацыі шайбы і вала і загадзя рознай таўшчыні і памеру для выбару мадэлі гідраўлічнага кіравання падчас зборкі.
Метад рамонту
Клапан сабраны метадам рамонту, дэталі могуць быць апрацаваны ў залежнасці ад эканамічнай дакладнасці, а затым пэўны памер з карэкціроўкай і эфектам кампенсацыі можа быць адрамантаваны падчас зборкі, каб дасягнуць зададзенай мэты зборкі. Напрыклад, засаўкі і клапан клапана клінавых варот, з -за высокай кошту апрацоўкі, каб рэалізаваць патрабаванні да абмену, большасць вытворцаў прымаюць працэс рамонту. Гэта значыць, у канчатковым шліфаванні паверхні герметызацыі засаўкі для кіравання памерам адтуліны пласціна павінна адпавядаць у залежнасці ад памеру адтуліны паверхні ўшчыльнення корпуса клапана, каб дасягнуць канчатковых патрабаванняў герметызацыі. Гэты метад павялічвае працэс супастаўлення пласціны, але значна спрашчае патрабаванні да дакладнасці папярэдняга працэсу апрацоўкі. Умелае дзеянне працэсу супастаўлення пласціны спецыяльным персаналам не паўплывае на эфектыўнасць вытворчасці ў цэлым. Працэс зборкі клапана: клапаны індывідуальна збіраюцца ў нерухомым месцы. Збор дэталяў і кампанентаў і Генеральная зборка клапанаў праводзяцца ў семінары зборкі, а ўсе неабходныя дэталі і кампаненты транспартуюцца на ўчастак зборкі. Звычайна, колькі груп работнікаў нясе адказнасць за зборку дэталяў і Генеральную Асамблею адначасова, што не толькі скарачае цыкл зборкі, але і палягчае прымяненне спецыяльных інструментаў зборкі і мае нізкія патрабаванні да тэхнічнага ўзроўню рабочыя.
Час паведамлення: 23-2022 лютага